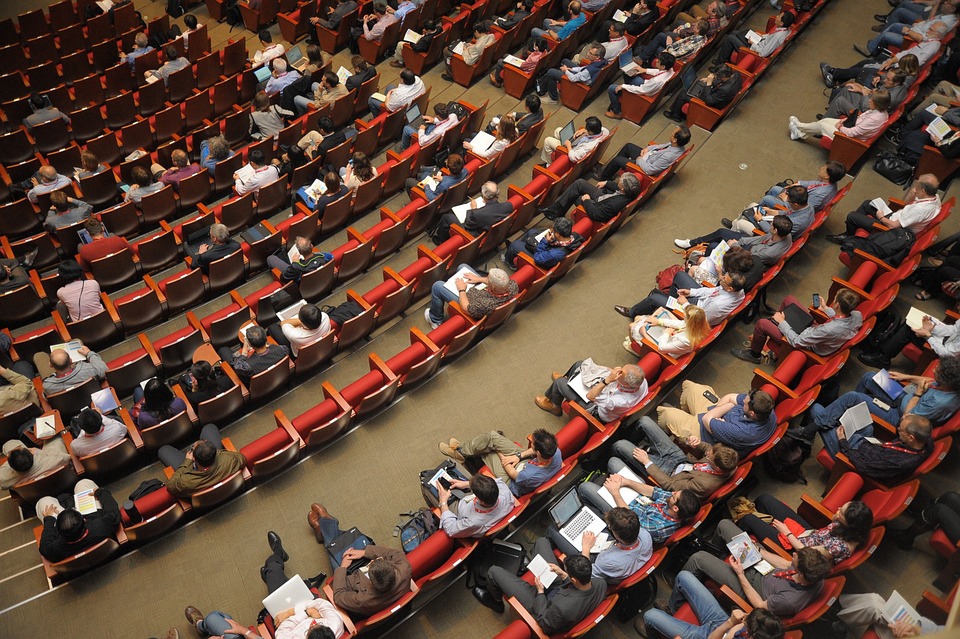
The Science of Audience Appeal: Techniques for Grabbing and Holding Attention
The Science of Audience Appeal: Techniques for Grabbing and Holding Attention
In a world that is bombarded with information and distractions, it can be challenging to grab and hold the attention of your audience. Whether you are a marketer, a public speaker, a content creator, or anyone else looking to connect with a group of people, understanding the science of audience appeal can be crucial to your success. By employing techniques that are proven to capture and retain the interest of your audience, you can increase the effectiveness of your communication and ultimately achieve your goals. In this article, we will explore some key strategies for enhancing your audience appeal.
Understanding the Brain’s Response to Stimuli
To effectively capture the attention of your audience, it is essential to understand how the brain responds to different stimuli. Our brains are wired to seek out information that is novel, relevant, and emotionally engaging. When we encounter something that is new or interesting, our brains release dopamine, a neurotransmitter that is associated with pleasure and reward. This reaction motivates us to pay attention and engage with the stimulus.
To leverage this natural response, it is important to create content that is fresh, intriguing, and emotionally resonant. By presenting information in a way that is unexpected or unique, you can capture the attention of your audience and keep them engaged.
Creating a Compelling Story
One of the most effective ways to capture and hold the attention of your audience is by telling a compelling story. Stories are powerful tools for communication because they engage not only the rational mind but also the emotional centers of the brain. When we hear a story, our brain releases oxytocin, a hormone that is associated with bonding and trust. This biological response makes us more likely to connect with the storyteller and absorb the information being presented.
To create a compelling story, consider the following elements:
– A strong hook: Start your story with a provocative question, a surprising fact, or an emotional appeal to grab the attention of your audience from the outset.
– Conflict and resolution: Every good story has a conflict that needs to be resolved. By introducing tension and drama into your narrative, you can create a sense of urgency and keep your audience engaged.
– Emotional appeal: Use vivid language and sensory details to create an emotional connection with your audience. By appealing to their feelings and values, you can make your story more memorable and impactful.
Using Visual and Audio-Visual Elements
In addition to storytelling, visual and audio-visual elements can be powerful tools for capturing and retaining the attention of your audience. Our brains are highly responsive to visual stimuli, processing images much faster than text. By incorporating compelling visuals, such as photographs, videos, or infographics, into your content, you can enhance its appeal and make it more engaging.
Similarly, audio-visual elements, such as music, sound effects, and animations, can add an extra layer of interest to your presentation. By appealing to multiple senses simultaneously, you can create a more immersive and memorable experience for your audience.
When using visual and audio-visual elements, it is important to keep in mind the principles of design and multimedia production. Ensure that your visuals are clear, relevant, and aesthetically pleasing, and that your audio-visual elements enhance rather than distract from your message.
Engaging Your Audience through Interactivity
Another effective strategy for capturing and holding the attention of your audience is by incorporating interactivity into your presentation. Interactive elements, such as polls, quizzes, demonstrations, or Q&A sessions, can foster active engagement and participation from your audience.
By inviting your audience to interact with your content, you can create a sense of agency and ownership that can increase their investment in your message. Additionally, interactive elements can provide valuable feedback and insights that can help you tailor your communication to better meet the needs and interests of your audience.
Conclusion
In conclusion, the science of audience appeal offers a wealth of strategies for capturing and holding the attention of your audience. By understanding how the brain responds to stimuli, creating compelling stories, using visual and audio-visual elements, and incorporating interactivity, you can enhance the effectiveness of your communication and increase the impact of your message.
By employing these techniques, you can create content that is engaging, memorable, and persuasive, ultimately achieving your goals of connecting with and influencing your audience. So next time you are preparing to communicate with a group of people, remember the science of audience appeal and use it to your advantage.
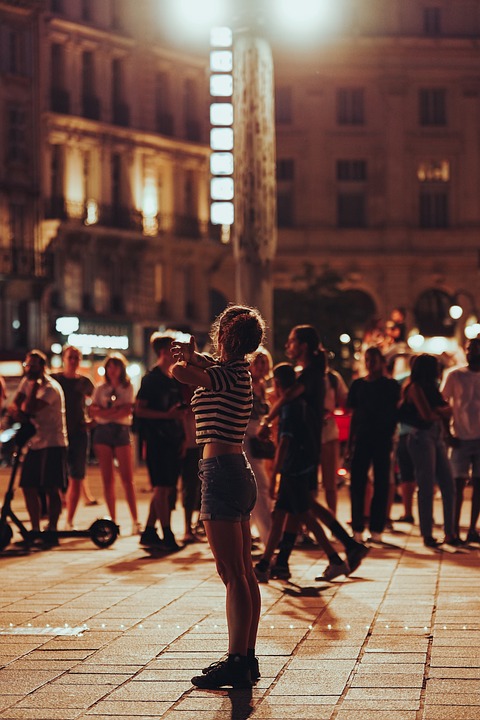
Creating Content that Resonates: A Guide to Captivating Your Audience
Creating Content that Resonates: A Guide to Captivating Your Audience
In today’s fast-paced world, grabbing the attention of your audience is more challenging than ever. With an abundance of content available at their fingertips, it’s essential to create content that not only stands out but also resonates with your target audience. In this guide, we will explore tips and techniques for creating content that captivates and engages your audience.
Know Your Audience
The first step in creating content that resonates with your audience is to know who your audience is. Understanding the demographics, interests, and behaviors of your target audience will help you tailor your content to meet their needs and preferences. Conducting market research, surveys, and analytics can provide valuable insights into your audience’s preferences and expectations.
Identify Your Unique Value Proposition
Once you have a clear understanding of your audience, it’s essential to identify your unique value proposition. What sets your content apart from the competition? What value does it provide to your audience? Defining your unique value proposition will help you create content that is not only relevant but also compelling and engaging.
Create Compelling Headlines and Titles
The first thing your audience will see is your headline or title, so it’s crucial to make it attention-grabbing and compelling. Use strong language, numbers, and emotional triggers to pique the curiosity of your audience and entice them to click on your content. A great headline can make all the difference in capturing and retaining your audience’s attention.
Use Engaging Visuals
Incorporating visuals such as images, infographics, videos, and GIFs can enhance the appeal of your content and make it more engaging for your audience. Visual content is more likely to be shared and remembered than text-only content. Be sure to use high-quality visuals that are relevant to your content and align with your brand’s aesthetics.
Write Compelling and Readable Content
The quality of your writing is crucial in keeping your audience engaged. Write in a clear and concise manner, and avoid jargon or technical language that may confuse your audience. Break up your content into digestible chunks with subheadings, bullet points, and lists to improve readability. Use storytelling techniques to make your content more relatable and engaging.
Provide Value and Solve Problems
Your content should provide value to your audience by solving their problems, answering their questions, or addressing their needs. By positioning yourself as a helpful resource, you can build trust and credibility with your audience. Consider creating how-to guides, tutorials, case studies, or informative articles that offer practical solutions and insights.
Encourage Interaction and Engagement
Engage with your audience by encouraging comments, shares, likes, and feedback on your content. Respond to comments and messages promptly to show that you value their input and are listening to their needs. Consider hosting contests, polls, surveys, or live Q&A sessions to foster interaction and engagement with your audience.
Optimize for Search Engines
To ensure that your content reaches a wider audience, it’s essential to optimize it for search engines. Conduct keyword research to identify relevant keywords and phrases that your audience is searching for. Incorporate these keywords naturally into your content, headings, meta descriptions, and alt text to improve your organic search rankings.
Promote Your Content Across Channels
Once you have created compelling content, it’s crucial to promote it across various channels to reach your target audience. Share your content on social media platforms, email newsletters, industry forums, and relevant websites to increase visibility and engagement. Consider collaborating with influencers, partners, or affiliates to amplify your reach and impact.
Track and Analyze Performance
Finally, track and analyze the performance of your content to understand what resonates with your audience and what can be improved. Use analytics tools to monitor metrics such as website traffic, engagement, conversions, and bounce rates. Adjust your content strategy based on these insights to continuously optimize and refine your content for maximum impact.
In conclusion, creating content that resonates with your audience requires a deep understanding of their needs, preferences, and behaviors. By identifying your unique value proposition, crafting compelling headlines, using engaging visuals, and providing value, you can captivate and engage your audience. Encourage interaction, optimize for search engines, promote across channels, and track performance to ensure that your content effectively reaches and resonates with your audience. By following these tips and techniques, you can create content that captivates and inspires your audience for optimal engagement and success.
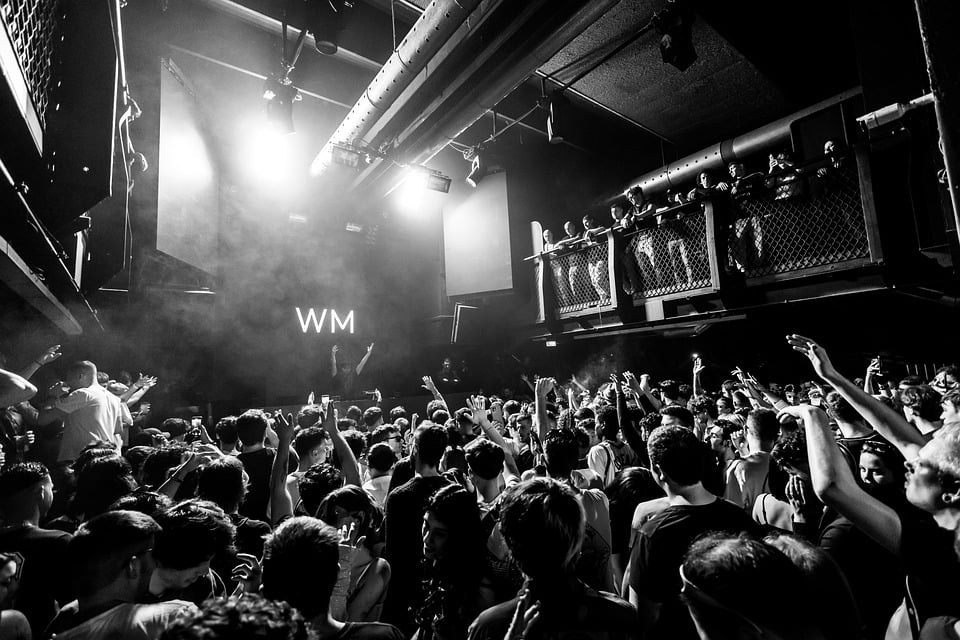
The Power of Audience Appeal: Strategies for Building a Strong Following
The Power of Audience Appeal: Strategies for Building a Strong Following
In today’s digital age, having a strong following can make or break a business or brand. With the rise of social media and online communities, attracting and retaining an audience has never been more crucial. But how can you effectively build a following that is engaged and loyal? In this article, we will explore different strategies for increasing audience appeal and building a strong following.
Know Your Audience
The first step in building a strong following is understanding who your audience is and what they are interested in. Take the time to research your target demographic, including their age, gender, interests, and online behavior. By understanding who your audience is, you can tailor your content and messaging to better resonate with them.
Create Valuable and Engaging Content
Once you have identified your target audience, the next step is to create content that they will find valuable and engaging. Whether it’s informative articles, entertaining videos, or inspirational photos, the key is to provide content that resonates with your audience and encourages them to interact with your brand.
Be Authentic and Genuine
In a world filled with advertising and marketing messages, audiences are craving authenticity. Be genuine in your interactions with your audience, whether it’s through social media, email newsletters, or in-person events. Building a strong following requires trust, and being authentic is key to gaining your audience’s trust.
Engage with Your Audience
Building a strong following is not just about creating content, but also about engaging with your audience. Respond to comments and messages on social media, participate in online discussions, and solicit feedback from your followers. By actively engaging with your audience, you can build a sense of community and loyalty around your brand.
Utilize Influencers and Collaborations
One effective strategy for increasing audience appeal is to work with influencers and collaborators who already have a strong following. By partnering with influencers in your industry or collaborating with other brands, you can tap into new audiences and expand your reach. Just make sure to choose influencers or collaborators whose values align with yours to maintain authenticity.
Offer Special Promotions and Discounts
To attract and retain your audience, consider offering special promotions and discounts to incentivize them to engage with your brand. Whether it’s a limited-time sale, a giveaway, or a loyalty program, providing value to your audience can help strengthen their connection to your brand and encourage repeat interactions.
Consistent Branding and Messaging
Building a strong following requires consistency in your branding and messaging. From your logo and color scheme to your tone of voice and values, make sure that your brand is consistently represented across all channels. Consistent branding helps build recognition and trust with your audience, ultimately leading to a stronger following.
Measure and Analyze Your Results
Finally, to build a strong following, it’s important to measure and analyze your results. Use analytics tools to track key metrics such as engagement rates, follower growth, and conversion rates. By analyzing your data, you can identify which strategies are working and optimize your efforts to continue building a strong following.
In conclusion, building a strong following requires a combination of understanding your audience, creating valuable content, and engaging with your audience authentically. By implementing these strategies and staying consistent in your branding and messaging, you can attract and retain a loyal following that will support your business or brand for years to come.
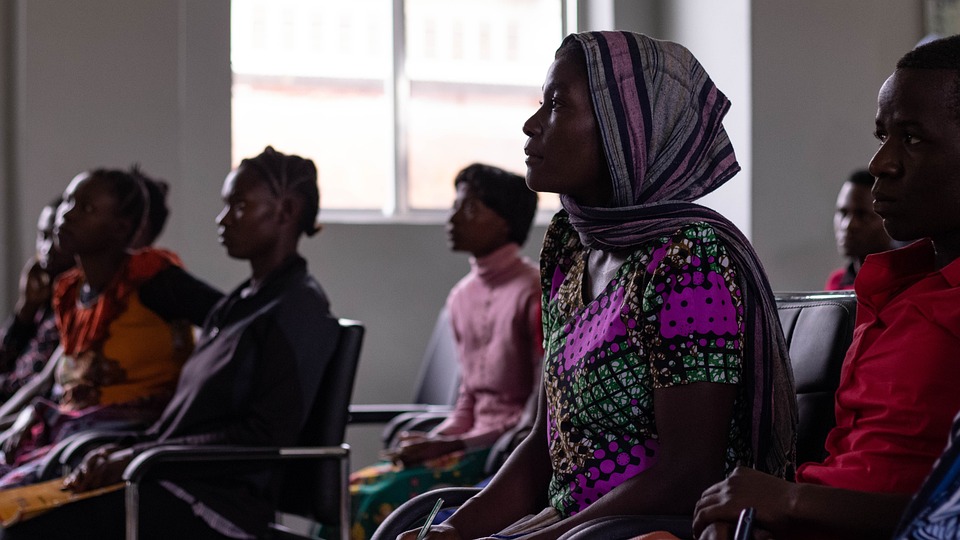
Understanding Audience Appeal: How to Engage and Retain Viewers
Understanding Audience Appeal: How to Engage and Retain Viewers
In today’s fast-paced digital age, capturing and retaining audience attention is becoming increasingly challenging. With the vast amount of content available online, viewers have the luxury of choosing what they want to watch and engage with. To succeed in this competitive landscape, content creators and marketers need to understand the key factors that drive audience appeal and engagement. This article will explore how to effectively engage and retain viewers by creating content that resonates with your target audience.
Know Your Audience
The first step in engaging and retaining viewers is to understand who your audience is. This includes demographic information such as age, gender, location, and interests, as well as psychographic details like values, attitudes, and behaviors. By developing a deep understanding of your audience, you can tailor your content to meet their needs and preferences.
One way to gather data about your audience is through analytics tools that provide insights into viewer demographics and behavior. Social media platforms like Facebook and Instagram offer detailed audience insights that can help you identify trends and preferences among your followers. By analyzing this data, you can create targeted content that is more likely to resonate with your audience.
Create Compelling Content
Once you have a clear understanding of your audience, the next step is to create compelling content that captures their attention. This includes producing high-quality videos, articles, infographics, and other types of media that are informative, entertaining, and visually appealing. The key is to provide value to your audience by offering content that educates, entertains, or inspires them.
When creating content, it’s important to keep in mind the preferences and interests of your audience. For example, if your target audience is young adults interested in fitness and health, you may want to create videos showcasing workout routines, healthy recipes, and wellness tips. By tailoring your content to meet the specific needs and interests of your audience, you can increase engagement and retention.
Interact with Your Audience
Engaging with your audience is essential for building a loyal following and retaining viewers. Encourage viewers to leave comments, ask questions, and provide feedback on your content. Respond to their comments and messages to show that you value their input and are listening to their needs. This two-way communication can help build a sense of community and foster a deeper connection with your audience.
In addition to responding to comments, consider hosting live Q&A sessions, polls, and contests to engage with your audience in real-time. These interactive activities can create a sense of excitement and exclusivity among your viewers, encouraging them to return for future content. By involving your audience in the content creation process, you can make them feel like a part of your brand and build a loyal following.
Optimize for SEO
Search engine optimization (SEO) plays a crucial role in attracting new viewers and retaining existing ones. By optimizing your content for search engines, you can increase your visibility in search results and drive organic traffic to your website or social media channels. Use relevant keywords, meta tags, and descriptions to improve your search engine rankings and make it easier for viewers to find your content.
In addition to keyword optimization, consider creating engaging titles, thumbnails, and descriptions that entice viewers to click on your content. Use eye-catching visuals, compelling storytelling, and a strong call-to-action to capture and retain audience attention. By combining SEO best practices with creative content creation, you can attract more viewers and keep them coming back for more.
Analyze and Iterate
Finally, it’s important to analyze the performance of your content and make adjustments based on viewer feedback and engagement metrics. Use analytics tools to track key performance indicators such as views, likes, shares, comments, and watch time. Identify trends and patterns in viewer behavior to understand what types of content are resonating with your audience and adjust your strategy accordingly.
Experiment with different types of content, formats, and distribution channels to see what works best for engaging and retaining viewers. A/B test your content to compare the performance of different variations and optimize for maximum engagement. By continuously analyzing and iterating on your content strategy, you can keep your audience engaged and loyal over time.
In conclusion, understanding audience appeal is crucial for engaging and retaining viewers in today’s competitive digital landscape. By knowing your audience, creating compelling content, interacting with your audience, optimizing for SEO, and analyzing and iterating on your content strategy, you can effectively engage and retain viewers. With the right approach, you can build a loyal following and drive long-term success for your brand or business.
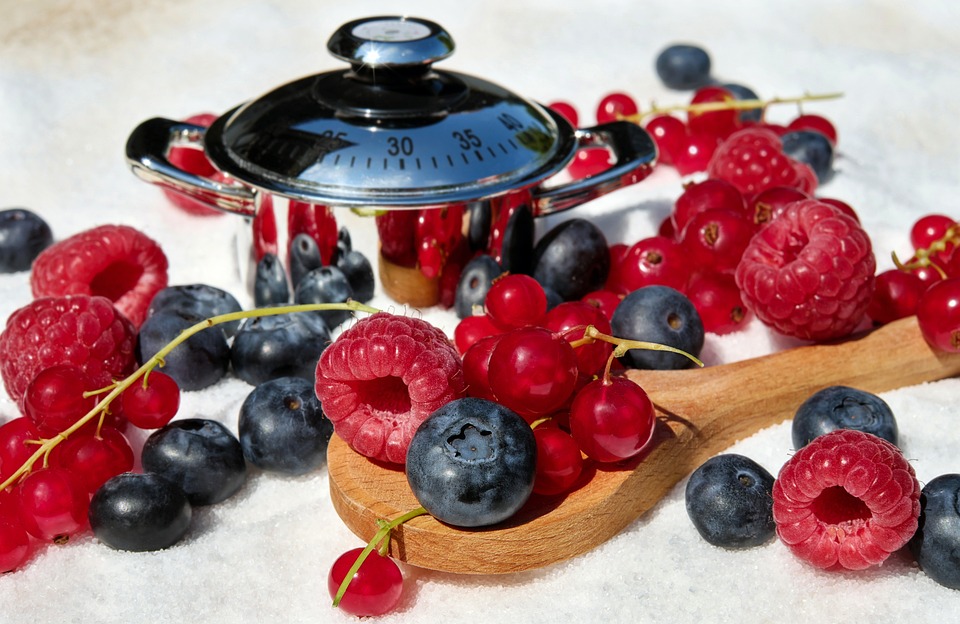
From Mixed Reception to Rave Reviews: Transforming Criticism into Praise
From Mixed Reception to Rave Reviews: Transforming Criticism into Praise
Introduction
Receiving criticism is never easy, especially when it comes to something that we have poured our heart and soul into. Whether it’s a piece of art, a project at work, or a personal endeavor, negative feedback can be difficult to swallow. However, turning criticism into praise is not only possible but can also be a valuable tool for growth and improvement. In this article, we will explore how to transform a mixed reception into rave reviews and use feedback to our advantage.
Understanding the Criticism
The first step in transforming criticism into praise is to understand the feedback that you have received. Take a moment to step back and objectively look at the critique. Is it specific and constructive, or is it vague and unhelpful? Understanding the root of the criticism is essential in order to address it effectively. Consider the source of the feedback as well – is it coming from a trusted mentor, colleague, or friend? Their perspective can provide valuable insights into areas of improvement.
Embrace a Growth Mindset
Instead of viewing criticism as a personal attack, try to embrace a growth mindset. See feedback as an opportunity to learn and improve, rather than a reflection of your worth or abilities. Remember that even the most successful individuals have faced criticism at some point in their careers. Use the feedback as a stepping stone towards progress and development.
Take Action
Once you have identified the areas of improvement, it’s time to take action. Create a plan to address the feedback and make changes accordingly. This may involve revising a project, seeking additional training, or reaching out to a mentor for guidance. Be proactive in implementing the necessary changes to turn the criticism into praise.
Solicit Additional Feedback
In order to truly transform criticism into praise, it’s important to solicit additional feedback. Reach out to others for their perspective on the revised work or project. This can provide valuable insights and help you gauge whether you have successfully addressed the initial critique. Be open to feedback and willing to make further adjustments if necessary.
Celebrate Successes
As you work towards transforming criticism into praise, don’t forget to celebrate your successes along the way. Recognize the progress that you have made and the improvements that you have implemented. Take pride in your ability to turn negative feedback into positive outcomes.
Turning Mixed Reception into Rave Reviews
By following the steps outlined above, you can turn a mixed reception into rave reviews. Embrace the feedback that you receive, view it as an opportunity for growth, and take action to address the areas of improvement. Solicit additional feedback, celebrate your successes, and continue to strive for excellence in all that you do. With perseverance and a positive attitude, you can transform criticism into praise and achieve success in your endeavors.
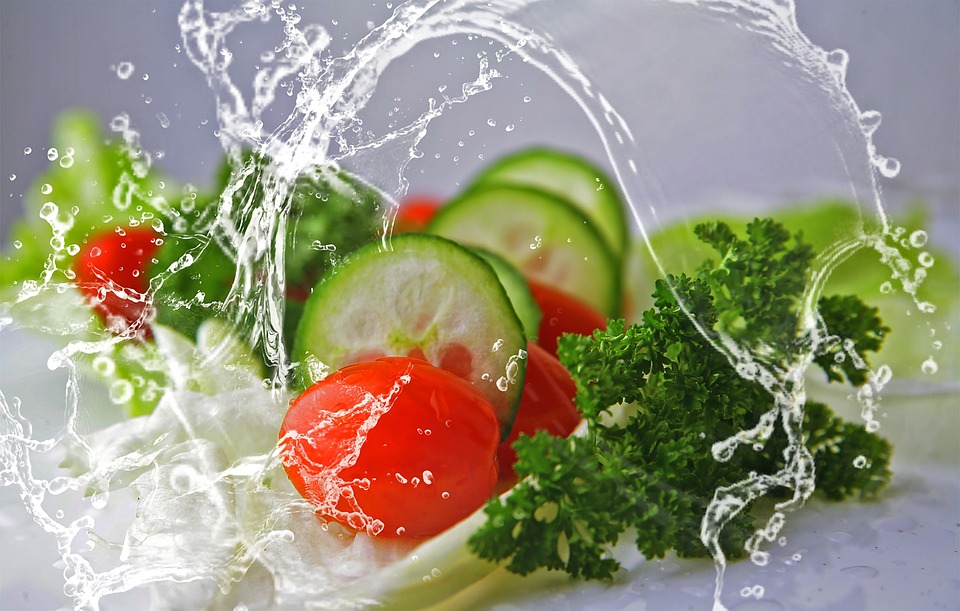
Exploring the Psychology Behind Mixed Reception: Unpacking the Dualities of Feedback
Exploring the Psychology Behind Mixed Reception: Unpacking the Dualities of Feedback
Feedback is a crucial component of communication and growth. It can shape our perceptions of ourselves and others, and influence our behavior and decisions. However, receiving feedback can be a complex experience, with individuals often experiencing mixed emotions and reactions to the feedback they receive. In this article, we will explore the psychology behind mixed reception of feedback, and unpack the dualities that can influence our reactions.
The Power of Feedback
Feedback is essential for learning and development. It provides individuals with information about their performance, behavior, or actions, allowing them to make adjustments and improvements. Feedback can come in various forms, such as praise, criticism, constructive suggestions, or evaluations. Positive feedback can boost self-esteem and motivation, while negative feedback can highlight areas for improvement and growth.
However, the impact of feedback can vary depending on how it is delivered, the context in which it is given, and the individual’s mindset and personality. Some people are more receptive to feedback, while others may feel threatened or defensive when receiving criticism. This diversity in reactions to feedback can lead to mixed reception, where individuals experience conflicting emotions and responses to the feedback they receive.
The Dualities of Feedback
When receiving feedback, individuals may experience a range of emotions and reactions that can be categorized into dualities. These dualities represent the conflicting and opposing forces that can influence our perceptions and responses to feedback. Some common dualities of feedback include:
1. Praise vs. Criticism: Positive feedback, such as praise, can boost self-confidence and motivation, while negative feedback, such as criticism, can highlight areas for improvement. Individuals may struggle with balancing the positive and negative aspects of feedback, leading to mixed reception.
2. Acceptance vs. Resistance: Some individuals may accept feedback with an open mind, willing to learn and grow from the information provided. Others may resist feedback, feeling defensive or threatened by the criticism. This duality can influence how individuals perceive and process feedback.
3. External vs. Internal: Feedback from others can shape our self-perceptions and behavior. External feedback can influence how we view ourselves and our abilities. However, individuals may also have internal feedback, such as self-criticism or self-doubt, that can conflict with external feedback and lead to mixed reception.
4. Growth vs. Fixed Mindset: Individuals with a growth mindset view feedback as an opportunity for learning and development. They welcome feedback as a way to improve and grow. In contrast, individuals with a fixed mindset may see feedback as a threat to their identity or abilities, leading to resistance and defensiveness.
Factors Influencing Mixed Reception
Several factors can influence how individuals receive and respond to feedback, leading to mixed reception. Some common factors include:
1. Personality: Individual differences in personality traits, such as openness, conscientiousness, and neuroticism, can shape how individuals respond to feedback. For example, individuals high in neuroticism may be more sensitive to criticism and react defensively, leading to mixed reception.
2. Self-Esteem: Individuals with low self-esteem may struggle with receiving feedback, feeling insecure or inadequate when faced with criticism. High self-esteem individuals, on the other hand, may be more resilient in the face of negative feedback, leading to mixed reception.
3. Relationship with Feedback Provider: The relationship between the feedback provider and receiver can influence the reception of feedback. Individuals may be more receptive to feedback from someone they trust and respect, while feedback from a perceived authority figure or stranger may be met with skepticism or defensiveness.
4. Context of Feedback: The context in which feedback is given can impact how it is received. Feedback given in a supportive and constructive manner may be more well-received than feedback delivered in a harsh or demeaning way. The timing, frequency, and specificity of feedback can also influence how individuals perceive and respond to feedback.
Managing Mixed Reception
To effectively manage mixed reception of feedback, it is important to develop self-awareness, resilience, and a growth mindset. Individuals can benefit from the following strategies:
1. Reflect on Feedback: Take the time to reflect on the feedback received, considering both the positive and negative aspects. Identify areas for improvement and growth, and develop a plan for addressing any concerns or suggestions provided.
2. Seek Clarification: If the feedback is unclear or confusing, seek clarification from the provider. Ask for specific examples or details to better understand the feedback and how it can be applied.
3. Practice Emotional Regulation: Manage emotions and reactions to feedback by practicing mindfulness, deep breathing, or other relaxation techniques. Acknowledge and validate your feelings, but also strive to maintain a rational and objective perspective on the feedback received.
4. Focus on Growth and Development: Embrace a growth mindset, viewing feedback as an opportunity for learning and improvement. Set goals for development and progress based on the feedback received, and track your progress over time.
In conclusion, feedback is a powerful tool for learning and growth, but it can also lead to mixed reception when individuals experience conflicting emotions and reactions to the feedback they receive. By understanding the psychology behind mixed reception and unpacking the dualities that can influence our responses to feedback, individuals can learn to manage and leverage feedback effectively for personal and professional development. By embracing self-awareness, resilience, and a growth mindset, individuals can navigate the complexities of feedback and use it as a catalyst for positive change.
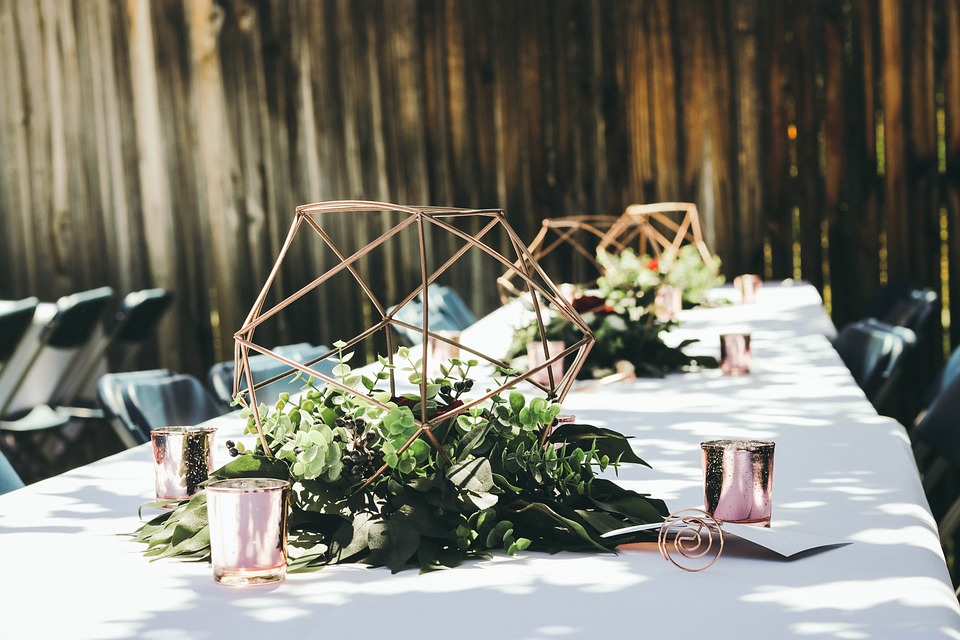
Turning Mixed Reception into Motivation: Harnessing Negative Feedback for Positive Change
Turning Mixed Reception into Motivation: Harnessing Negative Feedback for Positive Change
In life, we encounter moments where we receive feedback that may not always be positive. Whether it’s at work, in relationships, or from strangers, negative feedback can feel like a blow to our self-esteem and confidence. However, instead of letting it bring us down, we can choose to turn mixed reception into motivation and use it as a tool for positive change.
Understanding the Power of Feedback
Feedback, whether positive or negative, is essential for personal and professional growth. It provides us with insight into our strengths and weaknesses, helps us identify areas for improvement, and allows us to see ourselves from an outside perspective. While positive feedback can boost our confidence and validate our efforts, negative feedback can be just as valuable, if not more so, in helping us grow and improve.
When we receive negative feedback, it’s important to remember that it is not a reflection of our worth as individuals, but rather an opportunity for growth and self-improvement. By reframing how we view negative feedback, we can harness its power to fuel positive change in our lives.
Embracing Constructive Criticism
One of the keys to turning mixed reception into motivation is to embrace constructive criticism. Instead of viewing negative feedback as a personal attack, see it as an opportunity to learn and grow. Constructive criticism is meant to help us improve, not tear us down. By listening to and implementing feedback, we can enhance our skills, knowledge, and performance.
When receiving negative feedback, take a moment to reflect on the validity of the criticism. Ask yourself if there are areas where you can improve and what steps you can take to address them. Embrace feedback as a tool for self-improvement and use it to propel yourself forward.
Using Feedback as a Learning Opportunity
Negative feedback can be a powerful learning opportunity if we approach it with an open mind and a growth mindset. Instead of dwelling on the negativity, use feedback as a chance to reflect on your actions and behaviors. Ask yourself what you can learn from the feedback and how you can apply it to future situations.
By using feedback as a learning opportunity, you can turn negative experiences into positive outcomes. Take the time to analyze the feedback you receive, identify patterns or common themes, and use this information to make meaningful changes in your life. Remember, feedback is not meant to discourage you but to guide you towards growth and improvement.
Turning Criticism into Motivation
While negative feedback can be disheartening, it can also serve as a powerful motivator. Instead of letting criticism bring you down, use it as fuel to drive you towards positive change. Channel the energy from negative feedback into actionable steps towards self-improvement.
When faced with criticism, create a plan for how you can address the feedback and make meaningful changes. Set goals for yourself, seek support from others, and stay focused on your growth and development. Remember, criticism is not a roadblock but a stepping stone towards success.
Seeking Support and Guidance
Receiving negative feedback can be overwhelming, and it’s important to seek support and guidance from others during this time. Talk to friends, family, mentors, or colleagues about the feedback you’ve received and ask for their perspective. They can provide valuable insights, offer encouragement, and help you navigate through the challenges presented by negative feedback.
Surround yourself with positive influences who believe in your potential and can uplift you during difficult times. Seek out constructive feedback from trusted individuals who have your best interests at heart. Remember, you don’t have to face criticism alone – there are people who care about you and want to see you succeed.
Conclusion
Turning mixed reception into motivation is a powerful way to harness the power of negative feedback for positive change. By embracing constructive criticism, using feedback as a learning opportunity, turning criticism into motivation, and seeking support and guidance, you can transform negative experiences into opportunities for growth and self-improvement. Remember, feedback is a gift that can help you become the best version of yourself – all you have to do is open yourself up to the possibilities it presents.
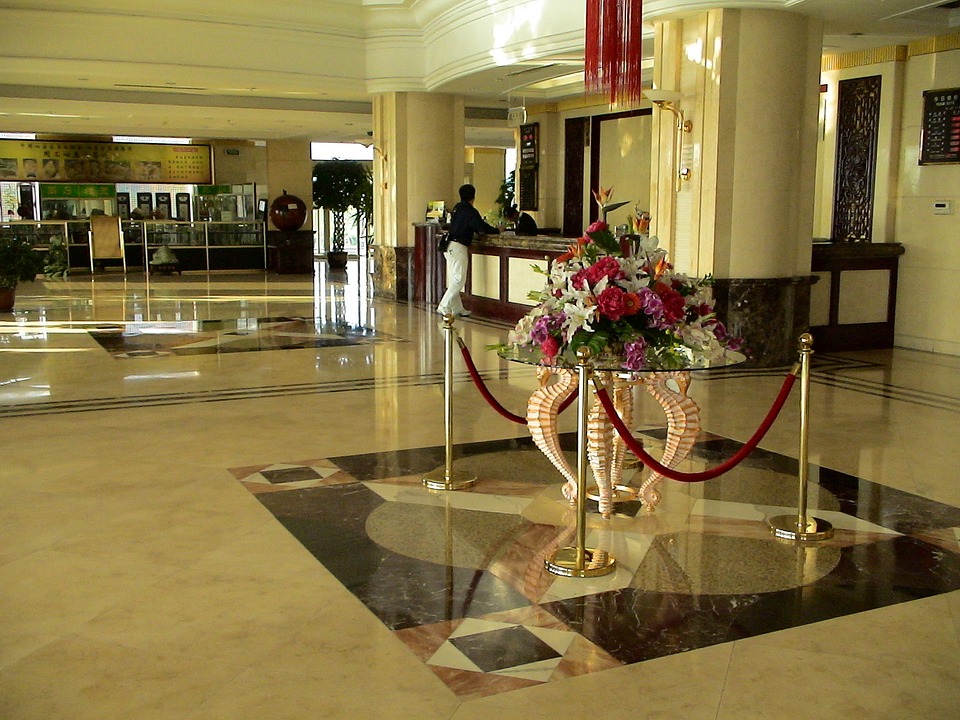
Overcoming the Fear of Mixed Reception: Strategies for Building Resilience
Overcoming the Fear of Mixed Reception: Strategies for Building Resilience
In our daily lives, it is common to seek approval and validation from others. Whether it be in our personal relationships, our professional careers, or our creative pursuits, we often fear the idea of receiving mixed reception from those around us. The fear of not being accepted or appreciated can be paralyzing, leading to self-doubt and anxiety. However, it is important to remember that not everyone will agree with or support us, and that is okay. In fact, embracing mixed reception can lead to personal growth and resilience. In this article, we will explore strategies for overcoming the fear of mixed reception and building resilience in the face of criticism.
Understanding the Fear of Mixed Reception
Before we can start to overcome the fear of mixed reception, it is important to understand where this fear comes from. The fear of not being accepted or appreciated by others is often rooted in a desire for validation and affirmation. We want to feel respected and valued by those around us, and when we encounter criticism or disapproval, it can shake our sense of self-worth. This fear is natural, but it can also be damaging if we allow it to control us.
Embracing Vulnerability
One of the first steps in overcoming the fear of mixed reception is to embrace vulnerability. Instead of trying to protect ourselves from criticism and rejection, we should be open to sharing our true selves with others. This means being willing to expose our weaknesses and imperfections, knowing that it is okay to not be perfect. By embracing vulnerability, we can build stronger connections with others and foster a sense of authenticity in our relationships.
Developing Self-Compassion
Another important strategy for building resilience in the face of mixed reception is to develop self-compassion. Instead of being overly critical of ourselves when we receive criticism, we should practice kindness and understanding towards ourselves. Self-compassion involves treating ourselves with the same care and empathy that we would offer to a close friend. By nurturing a sense of self-compassion, we can build resilience and bounce back from setbacks with greater ease.
Seeking Constructive Feedback
While receiving criticism can be challenging, it is important to remember that not all feedback is negative. Seeking out constructive feedback from others can help us identify areas for improvement and growth. Instead of fearing criticism, we should view it as an opportunity for learning and development. By seeking out constructive feedback, we can build resilience and adaptability in the face of mixed reception.
Cultivating a Growth Mindset
One of the key strategies for overcoming the fear of mixed reception is to cultivate a growth mindset. Instead of viewing criticism as a personal attack, we should see it as an opportunity for growth and development. A growth mindset involves embracing challenges, learning from failures, and persevering in the face of setbacks. By cultivating a growth mindset, we can build resilience and strength in the face of mixed reception.
Practicing Mindfulness
Mindfulness is another powerful tool for overcoming the fear of mixed reception. By practicing mindfulness, we can develop a greater awareness of our thoughts and emotions, allowing us to respond to criticism in a more calm and balanced manner. Mindfulness involves staying present in the moment, without judgment or attachment to our thoughts. By practicing mindfulness, we can build resilience and emotional strength in the face of mixed reception.
Focusing on What Matters Most
Ultimately, overcoming the fear of mixed reception involves focusing on what truly matters to us. Instead of seeking approval and validation from others, we should prioritize our own values and beliefs. By staying true to ourselves and our goals, we can build resilience and confidence in the face of criticism. Remember that not everyone will agree with or support us, and that is okay. By focusing on what matters most to us, we can overcome the fear of mixed reception and embrace the journey of personal growth and self-discovery.
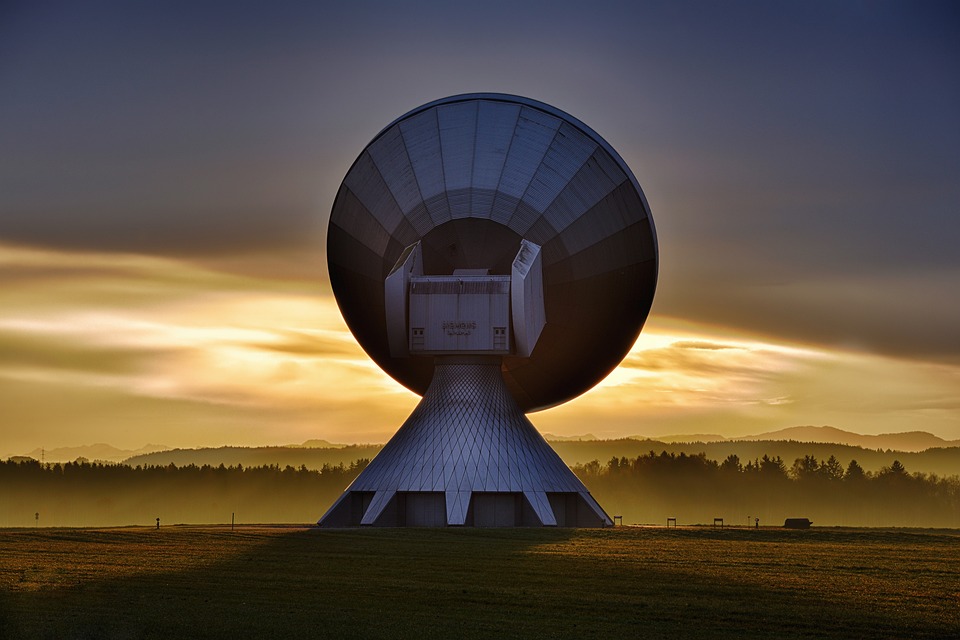
Why Mixed Reception Can be a Sign of Success and Innovation
Why Mixed Reception Can be a Sign of Success and Innovation
In today’s fast-paced world of technology and innovation, it is not uncommon for new ideas and products to receive a mixed reception from the public and industry experts alike. While some may see this as a failure, it can actually be a sign of success and innovation.
Breaking the Mold
When a new product or idea is introduced to the market, it is inevitable that it will be compared to existing products and ideas. If the new product or idea is too similar to what already exists, it may not generate much excitement or interest. However, if the new product or idea breaks the mold and presents something truly innovative and different, it may be met with skepticism or confusion at first.
This mixed reception is not necessarily a bad thing. In fact, it can be a sign that the new product or idea is pushing boundaries and challenging the status quo. By breaking away from the norm, innovators are paving the way for new possibilities and advancements in technology and society.
Creating Discussion and Debate
When a new product or idea receives a mixed reception, it often sparks discussion and debate among consumers, industry experts, and the media. This dialogue can be invaluable in driving innovation and improvements to the product or idea.
Critics may point out flaws or shortcomings that the innovators had not considered, leading to further refinement and development. Supporters may offer ideas for how the product or idea can be improved or expanded upon. By fostering discussion and debate, a mixed reception can lead to valuable feedback that ultimately helps the product or idea succeed.
Appealing to Different Audiences
Not everyone will have the same opinion when it comes to a new product or idea. Some consumers may immediately see the value and potential in the innovation, while others may be more hesitant or resistant to change. This diversity of opinions can result in a mixed reception.
Appealing to different audiences is essential for the success of any new product or idea. By generating interest and excitement among a variety of consumers, innovators can reach a wider market and increase the chances of their idea taking off.
Pioneering New Territory
Innovation often involves venturing into uncharted territory and taking risks that others may shy away from. This can result in a mixed reception as people are unsure of what to make of the new idea or product.
However, pioneering new territory is necessary for progress and advancement. By pushing boundaries and exploring new possibilities, innovators are laying the groundwork for future innovations and discoveries. The mixed reception they receive is a testament to their willingness to take risks and think outside the box.
Adapting and Evolving
When faced with a mixed reception, innovators have a choice – they can either give up and walk away, or they can adapt and evolve their idea to better meet the needs and expectations of their audience.
Adapting and evolving is a crucial part of the innovation process. By listening to feedback and making adjustments as needed, innovators can improve their product or idea and increase its chances of success. This willingness to learn and grow from feedback is a key indicator of success and innovation.
Overcoming Challenges and Obstacles
Innovation is not without its challenges and obstacles. A mixed reception can be one of these challenges, as it can be disheartening to see your idea met with skepticism or criticism.
However, overcoming these challenges is essential for success. By persevering in the face of adversity and staying true to their vision, innovators can prove the naysayers wrong and demonstrate the value of their idea. The ability to overcome challenges and obstacles is a clear sign of innovation and determination.
In conclusion, a mixed reception should not be seen as a sign of failure, but rather as a sign of success and innovation. By breaking the mold, creating discussion and debate, appealing to different audiences, pioneering new territory, adapting and evolving, and overcoming challenges and obstacles, innovators can turn a mixed reception into a springboard for success. It is through this process of pushing boundaries and challenging the status quo that true innovation can thrive.
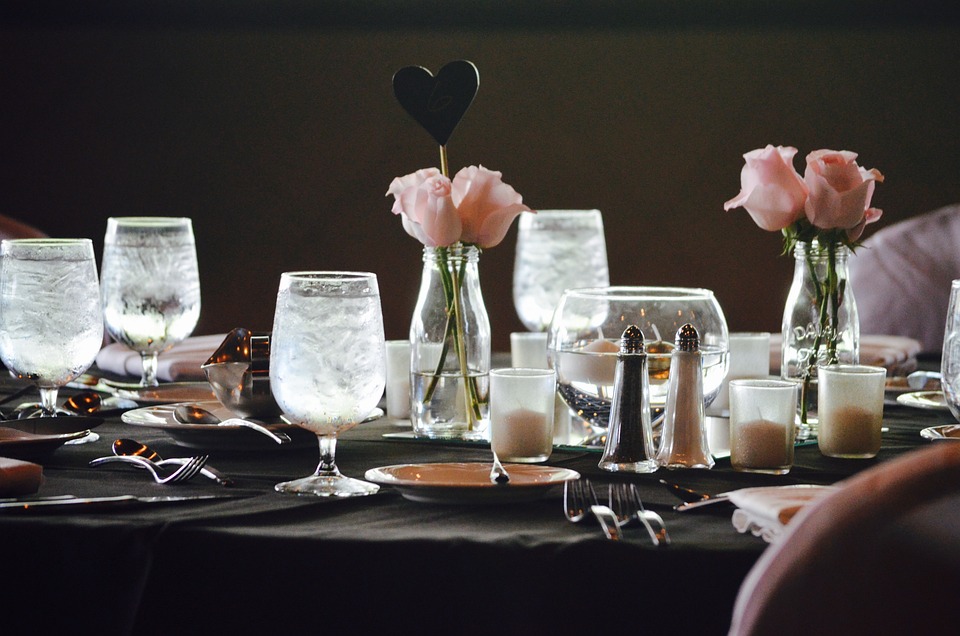
The Impact of Mixed Reception on Mental Health and Self-Esteem
The Impact of Mixed Reception on Mental Health and Self-Esteem
The Importance of External Validation
Receiving validation and recognition from others is essential for our mental well-being and self-esteem. When we receive positive feedback and affirmation from those around us, it reinforces our sense of self-worth and helps boost our confidence. However, what happens when the reception we receive is mixed or uncertain? This can have a significant impact on our mental health and self-esteem.
Understanding Mixed Reception
Mixed reception refers to a situation where the feedback we receive from others is a combination of positive and negative responses. For example, we may receive praise for our work from some individuals while others criticize or provide negative feedback. This can create a sense of uncertainty and confusion, leaving us unsure of how to interpret our own actions and abilities.
The Effects on Mental Health
When faced with mixed reception, individuals may experience heightened levels of stress, anxiety, and self-doubt. The conflicting feedback can lead to feelings of confusion and insecurity, as individuals struggle to make sense of the conflicting messages they are receiving. This can negatively impact mental health and lead to increased levels of worry and emotional distress.
Additionally, individuals may become more susceptible to negative thinking patterns and self-criticism. Constantly questioning their abilities and worth, individuals may struggle with feelings of inadequacy and low self-esteem. This can contribute to feelings of depression and a sense of hopelessness, as individuals may struggle to find a sense of validation and acceptance in their interactions with others.
The Impact on Self-Esteem
Mixed reception can have a profound impact on an individual’s self-esteem. When faced with conflicting feedback from others, individuals may begin to question their own worth and abilities. This can lead to a decline in self-esteem, as individuals may struggle to find a sense of validation and acceptance in their interactions with others.
Low self-esteem can have a ripple effect on various aspects of an individual’s life, affecting relationships, work performance, and overall well-being. Individuals with low self-esteem may avoid taking risks or pursuing new opportunities, out of fear of failure or rejection. This can limit their potential for growth and development, as they may struggle to believe in their own abilities and potential.
Coping Strategies for Dealing with Mixed Reception
It is important for individuals facing mixed reception to develop healthy coping strategies to manage the impact on their mental health and self-esteem. Here are some tips for dealing with mixed reception:
Seek Support
Reach out to friends, family members, or mental health professionals for support and guidance. Talking about your feelings and experiences can help you gain perspective and clarity on the situation.
Practice Self-Compassion
Be kind and gentle with yourself. Avoid self-criticism and negative self-talk, and instead practice self-compassion and forgiveness.
Focus on Your Strengths
Remind yourself of your strengths and accomplishments. Focus on the positive feedback you have received and celebrate your achievements.
Set Boundaries
Establish clear boundaries with individuals who provide conflicting or negative feedback. Surround yourself with supportive and uplifting people who validate and appreciate you.
Seek Professional Help
If you are struggling to cope with the impact of mixed reception on your mental health and self-esteem, consider seeking professional help from a therapist or counselor. They can provide you with personalized support and guidance to help you navigate through this challenging time.
In conclusion, mixed reception can have a significant impact on an individual’s mental health and self-esteem. It is important for individuals facing mixed reception to develop healthy coping strategies and seek support to help them navigate through this challenging time. Remember that you are not alone, and there are resources and tools available to help you overcome the negative effects of mixed reception. Stay strong and believe in yourself.